Ceramic Filter for Particulate Reduction System
Diesel particulate filter is used to remove black smoke (PM e. G.: Hydrocarbons, soot) from diesel engine exhaust, being a great contribution to the environment because of dealing with the exhaust from diesel engines. The diesel particulate filter can be used in different industrial fields such as environment protection, petrol-chemistry, medicine manufacture, and metallurgy etc. It has good investment return and broad prospect. The system installed DPF (Diesel Particulate Filter) been examined for urban bus, forklift, truck & mining constructing equipment. With increasing appearance of diesel engine automobile, the particulate from emission, mainly carbon, enhances the pollution to the environment. Regulation for diesel engine, stipulating the particulate in diesel passenger cars emission should meet the criterion: Below 2.0g/mile. The diesel particulate filter is able to filter above 80% carbon smoke particulate. For practical application, it would be a great help to solve the problem of air pollution.
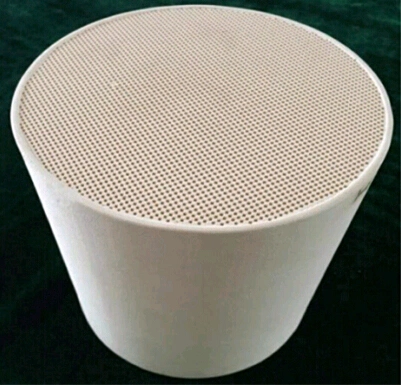
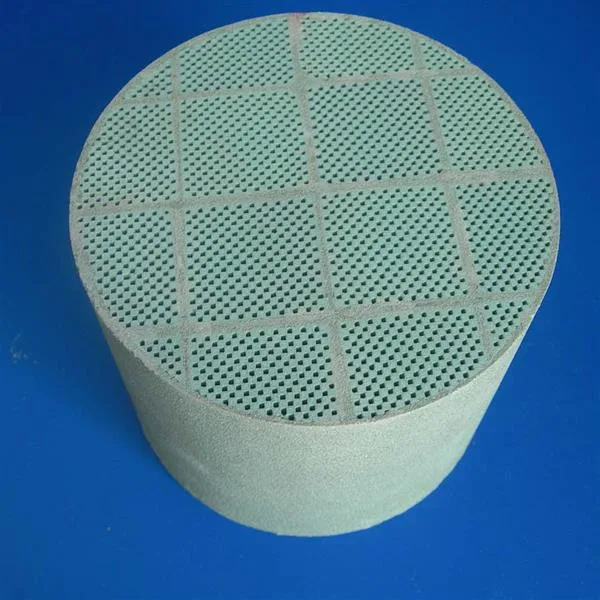
The particulate of emission is captured inside thin gas hole or entrance. As it lasts, the cumulated layer become thick, and pressure loss increase. To ensure the performance of engine, when pressure loss reaches some value, it is a must to recycle the filter. The recycle is making the particulate burning, by raising the gas temperature of filter. The particulate condition is related to the oxygen concentration. Normally, it is burning at 550-650. Its adopted to raise emission temperature by adjusting throttle, and increase gas temperature with burner. The particulate burning temperature can be decreased by catalyzed, making cumulative particulate burning as soon as possible, thus recover the pressure loss and fitters performance, then the filter is recycled.
Characteristics:
*Broad band filtration (the diameters of the filtered particles are 0.2-150 µ M)
*Low back pressure
*High filtration efficiency (can be up to70%-95%)
*High refractory
*High mechanical properties
*Special for diesel, and can provide the metal shell together
*High soot removal: >95%
Diesel Engine Exhaust
These filters have a cellular structure with individual channels open and plugged at opposite ends. Exhaust gases enter the open end, flow through the pores of the cell walls, and exit the filter through the adjacent channel. Soot particles are too large to flow through the pores, and they collect on the channel walls. Periodically the filter is regenerated (heated) to consume the soot and clean the filter.
Diesel particulate filter is used to remove black smoke (PM e. G.: Hydrocarbons, soot) from diesel engine exhaust, being a great contribution to the environment because of dealing with the exhaust from diesel engines. The diesel particulate filter can be used in different industrial fields such as environment protection, petrol-chemistry, medicine manufacture, and metallurgy etc. It has good investment return and broad prospect. The system installed DPF (Diesel Particulate Filter) been examined for urban bus, forklift, truck & mining constructing equipment. With increasing appearance of diesel engine automobile, the particulate from emission, mainly carbon, enhances the pollution to the environment. Regulation for diesel engine, stipulating the particulate in diesel passenger cars emission should meet the criterion: Below 2.0g/mile. The diesel particulate filter is able to filter above 80% carbon smoke particulate. For practical application, it would be a great help to solve the problem of air pollution.
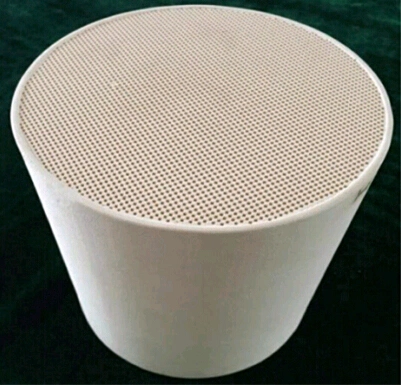
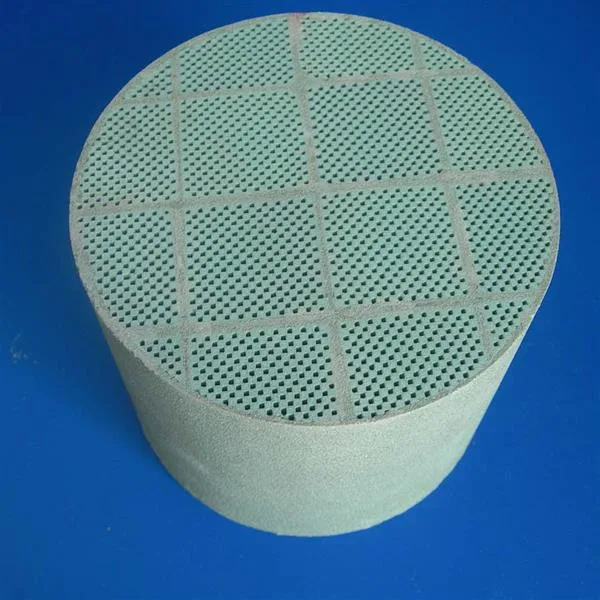
The particulate of emission is captured inside thin gas hole or entrance. As it lasts, the cumulated layer become thick, and pressure loss increase. To ensure the performance of engine, when pressure loss reaches some value, it is a must to recycle the filter. The recycle is making the particulate burning, by raising the gas temperature of filter. The particulate condition is related to the oxygen concentration. Normally, it is burning at 550-650. Its adopted to raise emission temperature by adjusting throttle, and increase gas temperature with burner. The particulate burning temperature can be decreased by catalyzed, making cumulative particulate burning as soon as possible, thus recover the pressure loss and fitters performance, then the filter is recycled.
Characteristics:
*Broad band filtration (the diameters of the filtered particles are 0.2-150 µ M)
*Low back pressure
*High filtration efficiency (can be up to70%-95%)
*High refractory
*High mechanical properties
*Special for diesel, and can provide the metal shell together
*High soot removal: >95%
Diesel Engine Exhaust
These filters have a cellular structure with individual channels open and plugged at opposite ends. Exhaust gases enter the open end, flow through the pores of the cell walls, and exit the filter through the adjacent channel. Soot particles are too large to flow through the pores, and they collect on the channel walls. Periodically the filter is regenerated (heated) to consume the soot and clean the filter.
Component | Unit | Data | Component | Unit | Data |
SiO2 | wt% | 48-51 | Fe2O3 | wt% | <0.5 |
Al2O3 | wt% | 31-34 | Na2O | wt% | <0.5 |
MgO | wt% | 14-16 | K2O | wt% | <0.5 |
Property (uncatalyzed) | 100/17 | 200/12 | |
Cell density | cpsi | 100 | 200 |
cpscm | 15.5 | 31.0 | |
Wall thickness | inch | 0.017 | 0.012 |
mm | 0.432 | 0.305 | |
Open frontal area (OFA), % | 34.5 | 34.5 | |
Geometric surface area (GSA) | Inch2 | 33.3 | 47.0 |
m2/l | 1.31 | 1.85 | |
Hydraulic diameter | Inch | 0.083 | 0.059 |
mm | 2.11 | 1.49 | |
Modulus of rupture (psi/cpscm) | 350 | 300 | |
Porosity (%) | 48 | 48 | |
Coefficient of thermal expansion 102 cm/cm/ (20-800) --maximum average | 5 | 5 | |
Mean pore size (micron) | 13 | 13 | |
Melting temperature ( Degree C ) | 1460 | 1460 |
Size(Diameter × length) | Cell density | Shape | |
mm | Inches | ||
Φ 118.4 × 101.6 | Dia.4.66 × 4 | 100/200CPSI | Round |
Φ 118.4 × 152.4 | Dia.4.66 × 6 | 100/200CPSI | Round |
Φ 127 × 152.4 | Dia.5 × 6 | 100/200CPSI | Round |
Φ 144 × 101.6 | Dia.5.66 × 4 | 100/200CPSI | Round |
Φ 144 × 150 | Dia.5.66 × 5.9 | 100/200CPSI | Round |
Φ 144 × 152.4 | Dia.5.66 × 6 | 100/200CPSI | Round |
Φ 144 × 254 | Dia.5.66 × 10 | 100/200CPSI | Round |
Φ 150 × 150 | Dia.5.9 × 5.9 | 100/200CPSI | Round |
Φ 190 × 200 | Dia.7.48 × 7.87 | 100/200CPSI | Round |
Φ 190 × 203 | Dia.7.48 × 8 | 100/200CPSI | Round |
Φ 228 × 305 | Dia.8.97 × 12 | 100/200CPSI | Round |
Φ 240 × 100 | Dia.9.45 × 3.94 | 100/200CPSI | Round |
Φ 240 × 240 | Dia.9.45 × 9.45 | 100/200CPSI | Round |
Φ 240 × 305 | Dia.9.45 × 12 | 100/200CPSI | Round |
Φ 260 × 305 | Dia.10.23 × 12 | 100/200CPSI | Round |
Φ 267 × 305 | Dia.10.50 × 12 | 100/200CPSI | Round |
Φ 286 × 267 | Dia.11.26 × 10.50 | 100/200CPSI | Round |
Φ 286 × 305 | Dia.11.26 × 12 | 100/200CPSI | Round |
Φ 286 × 355 | Dia.11.26 × 13.97 | 100/200CPSI | Round |
Φ 286 × 381 | Dia.11.26 × 15 | 100/200CPSI | Round |
Φ 203.3 × 97 × 152.4 | 8 × 3.82 × 6 | 100 CPSI | Race track |
Φ 203.3 × 97 × 254 | 8 × 3.82 × 10 | 100 CPSI | Race track |
Φ 188 × 103 × 145 | 7.4 × 4.05 × 5.7 | 100 CPSI | Race track |
Φ 191 × 95 × 152.4 | 7.52 × 3.74 × 6 | 100 CPSI | Race track |
Φ 374 × 270 × 317 | 14.72 × 10.62 × 12.48 | 100 CPSI | Assemble track |